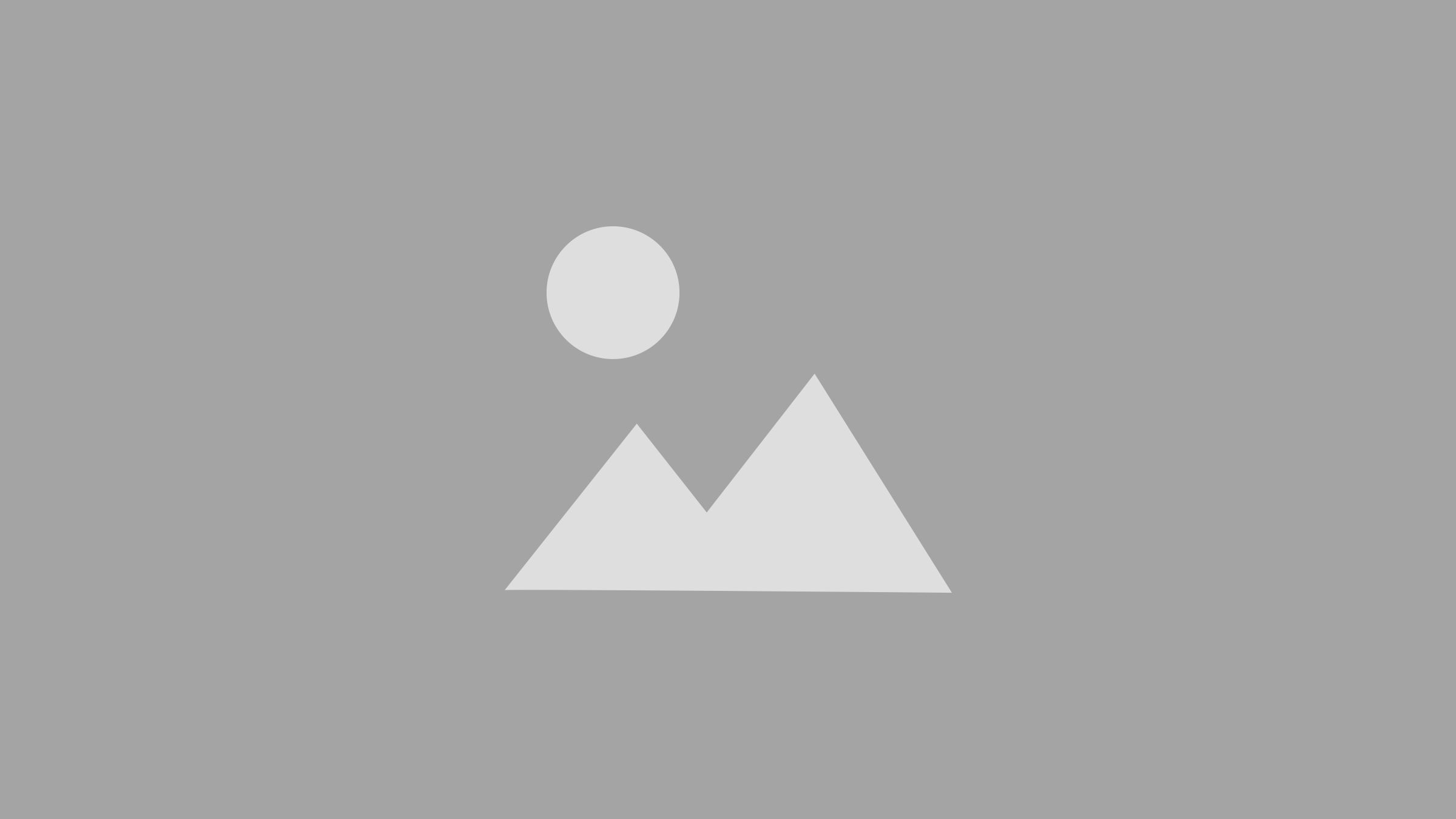
Read the latest news about innovative developments and applications with our original grey Neopor®, and news on the classic Styropor®.
At the Creation Center, BASF employees work hand in hand with customers to create innovations together. That is why it was important to the architect Bernadette Stauder-Buschlinger during the planning of the construction that products which stand for innovation and sustainable further development are used: the biomass balance products Neopor® BMB and Styrodur® BMB from BASF.
Subscribe to our Newsletter and win!
As a subsriber to our newsletter Styropor® > Neopor® > learn more you will receive interesting news and facts about our EPS products for the construction and packaging sector once a month.
At the Renovate Europe Day end of 2019 in Brussels, Belgium, exemplary renovation projects such as the energy-efficient Brunck district construction project in Ludwigshafen, Germany, were honoured at the European Parliament by experts in sustainable construction. The workers’ housing estate from the 1930s underwent integrated energy-efficient renovation between 1997 and 2006. At the heart of this renovation in Ludwigshafen was the facade insulation with insulation materials made of Neopor®, which reduces CO2 emissions and cuts heating costs thanks to its excellent insulation performance.
Not only energy efficient living was important for the future occupants of the houses - they also wanted the environmental impact of the materials used in construction to be kept to a minimum. By using low carbon EPS made of Neopor® BMB both specifications could be achieved.
On BASF’s initiative, representatives from trade associations, politics, and the construction industry came together in Poland in September 2019 to discuss the industry’s role in tackling climate change.
Editor Florian Langenscheidt presents over 200 champions of German business, including the Styropor® brand from BASF, in the illustrated book Deutsche Standards—Marken des Jahrhunderts 2019 (German standards—brands of the century 2019), published by ZEIT Verlagsgruppe.
What is it that makes Styropor® such an iconic brand?
The international trade fair Klimahouse 2019 inspired its 36,000 visitors with ideas for energy-efficient building and renovation. BASF’s customers also presented their sustainable products at the event in Bolzano, Italy, from 23 to 26 January 2019—including Fornaci Laterizi Danesi, a manufacturer of insulating blocks with Neopor®.
BASF is increasing its global production capacity for Neopor® (expandable polystyrene containing graphite) by a total of 40,000 metric tons per year. Adjustments in the plants at the two production sites in Ludwigshafen, Germany, and Ulsan, Korea, will take place through the fourth quarter of 2018.
The alliance of five trade associations and four companies of the plastics industry stands for safe and sustainable building in Europe. The focus is on fire prevention.
With 35,000 visitors, Klimahouse 2018 – an international trade fair for energy-efficient building and renovation held in Bolzano, Italy – was a resounding success. At the event, a number of BASF’s customers demonstrated the great versatility of the graphitecontaining raw material Neopor®.
The new Styropor® P 24 Speed lives up to its name: Due to a lowered pentane content (∼4.8 per cent), moulding cycle and conditioning times are shortened during the production process. Compared to conventional Styropor® P 26, the moulding cycle time of the Speed version can be reduced up to 50 per cent. Furthermore, the new Styropor® P24 Speed is equipped with the usual quality features and is therefore perfect for food packaging. Electronic parts can also be transported safely in thin-walled technical packaging, produced out of Styropor® P 24 Speed.
The reports and articles on the future of construction featured in “Corpus - Constructing Tomorrow”, BASF’s multiple-awardwinning online magazine devoted to architecture, infrastructure and high-performance construction materials, are now also available on the BASF-Website. In its four sections – Architecture, Urban Environment, Ideas & Solutions and Infrastructure – readers can learn more about intelligent housing solutions, coastal protection, innovative materials and new research findings, as well as reading interviews with experts and finding out about construction and infrastructure projects.
On 5 October, the European Association for External Thermal Insulation Composite Systems (EAE) held the fourth European ETICS Forum in Warsaw. With a total of 270 participants from 25 countries, the event was a great success.
Owners of historical buildings often do not carry out energy efficiency renovations because they want to maintain an existing facade that is worth protecting or it is under a preservation order. Internal insulation with insulating panels made of Neopor® offers an environmentally friendly and cost effective alternative. Read about the advantages this offers and aspects to consider in the October issue of ausbau+fassade magazine.
Insulating with Neopor protects health – now also confirmed in Europe by GREENGUARD label certification. The raw material has already carried this labeling for healthy products for many years in the U.S.
Want to know how to insulate your flat roof efficiently and at low cost? Then read the current article "Insulation boards for the singlelayer, utilised flat roof" in the Ernst & Sohn special edition Flachdächer 2017. Find out more about what to consider when choosing the insulation material and why Neopor® is particularly suitable for the single-layer, utilised flat roof.
Due to its special material composition, the new Schöck Element Isokorb Combar XT minimizes thermal bridges on projecting building elements: While Isokorb insulating element consists of the highly efficient BASF insulating raw material Neopor®, the manufacturer has, for the first time, chosen Combar glass fibre bars for the tensile bars.
In the beginning of 2017, Neopor® broke through an extraordinary barrier. Since it was launched on the market in 1998, more than one million tons of this BASF innovation have been sold in Europe by the company from its site in Ludwigshafen, Germany. Insulation made of Neopor® has been used in around five million homes all over Europe – thereby making a substantial contribution to the reduction of CO2 emissions.
At the Bouwbeurs International Construction Exhibition in Utrecht (Netherlands), FALK presented the first PIR-based insulation product that is manufactured using the biomass balance approach from BASF with renewable resources.
What are the materials of the future? Does the scarcity of resources present an opportunity for new technologies? And how can sustainability and design be combined? These questions, among others, occupied the participants of the “Planning for the future” workshop on 17 November at BASF in Ludwigshafen.
BASF has developed a new technology for welding insulation boards. The contactless, thermal welding process makes it possible to combine different insulation boards like Styrodur®, Neopor®, Basotect® or SLENTEX®. The Styrodur® portfolio also includes new, especially thick boards made using this process.
End of October 2016, Kyoung-jin Cha, Head of Styrenic Foams Business at BASF Korea, has been honored with a presidential citation in celebration of the 8th Chemical Industry Day.
Five single- and multi-family houses, which have been renovated over the last five years, demonstrate that Neopor® is the optimal insulation material for refurbishing old buildings, in addition to offering a good cost-benefit ratio.
BASF’s Neopor® is the product of choice for Betonrossi, Italy, to make Neoisolbeton™ – a lightweight and thermally insulating mortar, which can be used as a filler below the screed in floor and flat roof substrates. Neoisolbeton™ is considerably lighter than traditional cement-based mortar and has a thermal conductivity of 0.068 W/(m·K).
Globally only with Polymeric FR. After Europe, Korea, and the USA, the transition now also followed in China: since the end of 2015, all of the Styropor and Neopor® insulation materials from BASF around the world contain the polymeric, plastic-like flame retardant Polymeric FR.
A seven meter car made of Neopor® was the most spectacular object at the third “fabriktag” of BASF’s designfabrik .
Watch our video and learn more about Neopor® and its possibilities in flat roofs. We show how the powerful insulation material is used to insulate the new BASF office building.
Neopor®’s exemplary eco-efficiency greatly improves the overall sustainability assessment of buildings. Compared with other insulation materials such as mineral wool, Neopor® offers the best eco-efficiency. The special properties of Neopor® make it possible to reduce insulation thicknesses and raw material consumption. As a result, the environment is protected while still achieving maximum insulation performance – at a comparatively low cost.
Special Recognition in the German Property Developer Prize for Hohenzollern-Höfe in Ludwigshafen/Germany. The heritageprotected buildings receive a renovation of the energy systems by using an external thermal insulation composite system (ETICS) made of Neopor®.
In the new office building in Ludwigshafen BASF is using the powerful insulation material Neopor® and thus fulfills its own high requirements for sustainable construction.
BASF extends its Neopor® portfolio, presenting the newly developed Neopor® F 5 PRO, optimized for perimeter and flat roof insulation.